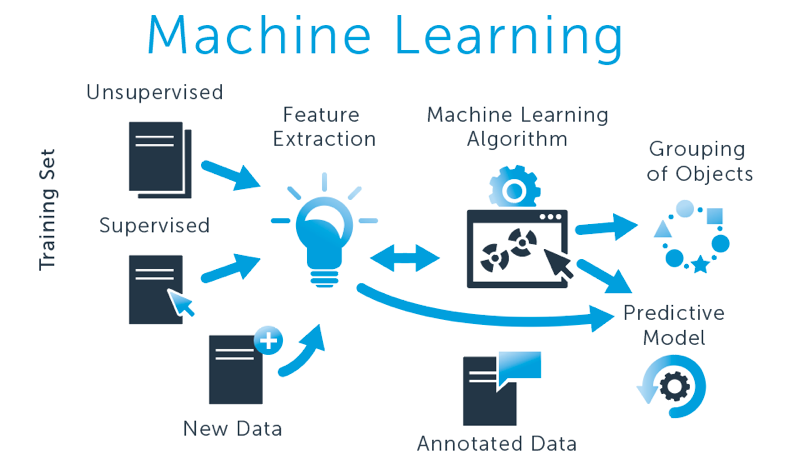
Developing and Implementing a Safety Lead Indicator Program
Organisations are increasingly moving towards an approach to safety that is proactive and predictive. For this to occur, a socio-technical systems approach to safety is often recommended. This involves considering all variables within the work environment and how they interact with one another (e.g., people, procedures, systems, leadership, and strategy). In this sense, safety indicators should measure and/or facilitate the presence of organisational factors8 12.
Lehtinen and Wahlstrom10categorised different types of safety management which contribute to performance management into three areas:
- Plant and equipment: designed “fit for purpose” in order to reduce risk occurring
- Systems and procedures: designed to ensure equipment is operated and maintained appropriately
- People: possess the relevant knowledge, skills and abilities to operate plant and equipment, and to implement systems and procedures
Leading versus Lagging Indicators
An indicator can be defined as any qualitative or quantitative measure which provides information on safety performance. There are two main types of safety indicators used by organisations to monitor and/or improve their level of safety, referred to as lagging and leading indicators. Lagging indicators are reactive by nature, measuring the end-result of an activity. They are generally organisation-level measures which could be classified as accomplishments, results or outcomes. Common examples of lagging indicators used by organisations include the recorded number of injuries, lost-time frequencies, number of investigations conducted following incidents, and dollar value of workers’ compensation claims4 12 14.
Leading indicators on the other hand are proactive measures, providing information which allows an organisation to anticipate a change in safety performance. They can be behaviours, processes or actions related to safety, allowing the end-user to respond to said change in order to reduce risk/threat4 12 14.
When you compare the two, lagging indicators signify that action needs to be taken with regard to safety performance, whereas leading indicators highlight where that action needs to occur. Importantly, lagging indicators do still hold significance and can be used to confirm (or disconfirm) the validity of leading indicators8 16. Figure 2 below illustrates this difference.
Figure 1. Graphical depiction of leading versus lagging safety indicators6
Types of Leading Indicators
Leading indicators are commonly described as safety metrics that are associated with safety performance. They describe an “ideal state” which the organisation is aiming to achieve and therefore aid risk assessment and risk management12 18.
The Swiss Cheese Model11is commonly used to describe how a problem/error can result in an accident occurring. The model is based on the premise that when a problem occurs it cascades through a series of organisational, technical and procedural “defensive barriers”. Each of these barriers has ‘holes’ and when a problem cascades through all of these holes (i.e., the holes line up with one another) an accident will occur. If however these holes are addressed in ample time the accident can be avoided3 11 14. Wang14describes leading indicators as types of organisational and human factors that can act as defensive barriers. Therefore monitoring these indicators allows a problem to be identified before accidents occur. As outlined below, there are a number of types of leading indicators.
Monitor Indicators versus Drive Indicators
Monitor indicators refer to an organisation’s potential to achieve safety by indirectly measuring performance. An example of this type of indicator is ‘Safety Motivation’ which could be measured via the extent employees’ consider safety to be a value which guides their behaviour at work. On the other hand, drive indicators relate to activities/actions taken by an organisation in order to improve safety. An example of a drive indicator is ‘Safety management and leadership’ which could be measured via the number of walk-throughs management does per month, or the extent management is viewed as committed and involved in safety activities12.
Objective Indicators versus Subjective Indicators
Objective leading indicators are calculated through correlating safety metrics with safety performance data. As the name suggests, they are the most objective type of indicator and can be measured at the individual, group and organisational-level. Importantly, this type of indicator can still be manipulated or skewed depending how the information is recorded and they also may not capture the quality of the safety system. Subjective indicators are based on values, attitudes and behaviours of people measured and can be used to validate reasons behind changes in objective indicators, or to identify a metric not yet measured by the organisation. For use in a safety program, subjective indicators require conversion to a metric form. Both types are therefore useful as part of a safety management program2 3 7.
Positive Indicators versus Negative Indicators
Positive indicators measure desirable states that an organisation wishes to achieve (e.g., frequency of supervisor walk-throughs, level of employee empowerment). Conversely, negative indicators measure the undesirable (e.g., frequency of loss of separations, frequency of errors reported). Leading indicators can be either positive or negative, whereas lagging indicators are always negative15.
Characteristics of an Effective Leading Indicator
Common guidelines for developing leading indicators are outlined below4 5 8 14:
- Ensure the indicator is easy to understand and represents an important aspect of the organisation’s safety management system;
- Indicators should address aspects of the organisation that have the capacity to be improved (i.e., they should not be measured just for the sake of it);
- There should be more positive than negative indicators measured, as negative indicators can deter incident reporting;
- Indicators should be both reliable (i.e., it provides the same output when measured repeatedly) and valid (i.e., it measures what it is intended to measure);
- Indicators should be cost-effective, in which the degree of time/energy spent measuring it is relative to its utility;
- Indicators and corresponding metrics should be regularly monitored and evaluated, as they will evolve over time based on changes in safety performance, as well as the business, technical and political environment they function in;
- Indicators should be customised to suit organisational-level and site-level characteristics
Further, The American Bureau of Shipping2suggests an organisation fulfils the following criteria before implementing a leading indicator program:
- The organisation is compliant with all relevant safety regulations;
- The organisation has identified that organisational factors and human error are the cause of the majority of operational incidents;
- There is a genuine desire within the organisation to prevent incidents;
- The organisation is relatively stable and not experiencing any major changes (e.g., mergers, acquisitions, reorganisations).
Organisational Safety Culture
It is important that a safety lead indicator program is aligned with the organisation’s safety climate and culture. Safety climate refers to the overarching attitudes and perceptions of employees about how safety is managed within their organisation. In contrast, safety culture encompasses an organisation’s systems, behaviours and perceptions relating to safety management. If an organisation is inherently reactive and slow to change their operations and structure, implementing an effective leading indicator approach to safety will be a challenging feat. Organisational safety climate surveys provide an opportune chance to measure and improve safety culture, and therefore serve as one type of leading indicator3 4 14.
Developing Leading Indicators
The above section summarised common types of leading indicators used by organisations to manage safety performance. This section focuses on how an organisation should develop and validate their leading indicators prior to implementation.
At a conceptual level, developing leading indicators involves first understanding the causes of accidents/error, then determining key steps to prevent this accident/error occurring, and lastly converting these steps into a measurable process13 14. As outlined previously, leading indicators are commonly defined as safety metrics that correlate with safety performance. The process therefore involves two key steps:
- Identifying significant safety factors that are critical to improving an organisation’s safety performance
- Identifying leading indicators (and corresponding metrics) that correlate with these safety factors
Grabowski and colleagues7conducted a detailed pilot study of applying the above process within a large marine transportation company. Through conducting a series of interviews, a set of organisational, group and individual level safety factors were identified as being important for improving their safety performance. Each of these safety factors were then validated by calculating the degree they each positively correlated with their respective safety performance measure (e.g., is hiring quality personnel significantly correlated with the number of accidents recorded). A statistical analysis called Confirmatory Factor Analysis was also conducted to ensure each of the safety factors were independent/distinct from one another, and to also determine the amount of variance each safety factor accounted for in the overall safety model7.
Following the above analyses, a set of hypotheses were generated for each predicted correlation (e.g., Anonymous reporting by individuals will result in better safety performance). Both subjective and objective measures of safety performance (i.e., dependent variables) were used to validate the effectiveness of each leading indicator. Subjective measures were gathered via the organisation’s safety climate questionnaire. Objective measures included metrics such as number of accidents, incidents, near misses and LTI>=3. A leading indicator was deemed important if there was a significant correlation between itself and the relevant dependent variables. Interestingly, only the subjective measures of safety performance were found to have significant relationships with the safety factors. This however warrants further investigation of other types of objective measures7.
Grabowski and colleagues7summarised the process used as part of their pilot study in the following four steps:
- Develop safety factor hypotheses (via interviews with SMEs within the organisation and past empirical research)
- Collect objective safety performance and subjective safety climate information (i.e., dependent variables)
- Determine the relationship between each safety factor and its corresponding dependent variables, along with the effectiveness of the overarching safety factor model (via Confirmatory Factor Analysis)
- Identify a set of leading indicators for the organisation
The diagram below, produced by Wang14clearly outlines the steps involved and frames it in the context of being a continuous improvement process.
Figure 2. Framework for safety lead indicator development14
Feel free to contact us with any questions on how we can support your leading indicators program.
Cortexia: Leading Human Factors Consultancy Australia